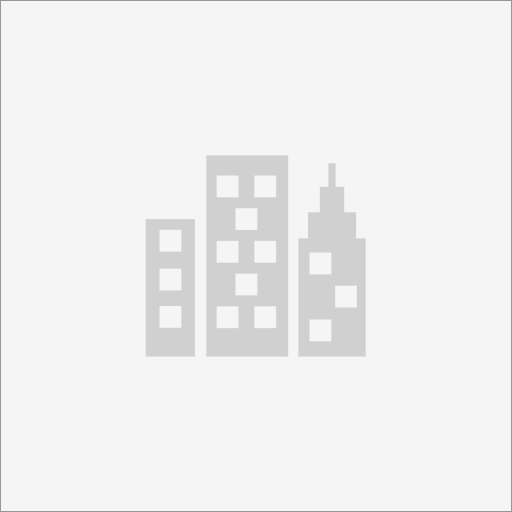
Unilever
vacanciesineu.com
Job Description
Job Title: Production Unit Shift Manager
Location (City, Country): Gloucester, UK
JOB PURPOSE
The production unit shift manager is responsible for the line management of operator teams and to deliver the safety, quality, efficiency & waste objectives for their area on shift.
KPIs & KAIs – OEE, Waste, Cost of Quality, D-Incidents, Housekeeping & Hygiene Scores, Safety Leading Indicators
RESPONSIBILITIES
- Technical / Functional – shift managers need to have a strong background in manufacturing. They should have a firm grasp on the principles of people leadership, continuous improvement, loss capture, safety standards, quality standards and incident management.
Safety
-
Action Completion – Works with the safety team and production coordinator to complete relevant actions from the safety action plan, including but not limited to machinery safety, incident investigations, CSHEC minutes, SBO/DCAs, near misses, SHEPAR.
-
Audits – Expected to carry out and follow up safety audits in line with site requirements.
-
Incident Management – expected to professionally manage safety incidents as they occur on shift, including but not limited to evacuations, injuries, near misses and high safety tags. This includes preparation and communication of relevant paperwork to the right quality.
-
Incident Investigations – carry out investigations for safety incidents that are isolated to their shift.
-
Safety Tags – expected to ensure teams are proactively raising safety tags to drive the continuous improvement agenda on site.
-
Training – working with the training department on site to ensure teams are trained in the relevant safety elements.
Quality
-
Action Tracking – Works with the safety team and production coordinator to complete relevant actions from the quality action plan, including but not limited to housekeeping & hygiene, incident investigations.
-
Audits – Expected to carry out and follow up quality audits in line with site requirements.
-
Incident Management – expected to professionally manage quality incidents as they occur on shift. This includes preparation and communication of relevant paperwork to the right quality.
-
Incident Investigations – carry out investigations for incidents in full that are isolated to their shift, in particular low-level ones.
-
Validation – expected to proactively drive and validate that quality checks are being carried out to the right standard and acted upon i.e. metal checks, CRQS, cleans, etc.
-
Quality Tags – expected to ensure teams are proactively raising quality tags to drive the continuous improvement agenda on site.
-
Training – working with the training department on site to ensure teams are trained in the relevant areas of quality.
-
Operational Decision Making – expected to make decisions on shift relating to quality & to escalate where appropriate.
Operational Activities:
-
Decision Making – Makes key decisions on shift and coordinates the factory activities with other shift managers.
-
Standards Enforcement – Responsible for enforcing site standards on behaviour, safety, quality, breaks and processes.
-
Team Governance – Responsible for providing governance and leadership for semi-autonomous teams on shift. The expectation is to develop these teams through guidance and coaching to a higher level of autonomy.
-
Performance Management – Expected to manage the performance of people on shift and intervene where this does not meet expectations.
-
Activity Execution & Oversight – Expected to ensure that production activities are carried out professionally in line with plans developed by day teams. Where necessary, it is expected that shift managers adapt & refine these plans to suit circumstances.
-
Production Sign Off – It is the shift manager’s responsibility to sign off resumption of production after significant periods of downtime.
-
Disruption Communication – Clearly communicating any changes to the plan that need to occur or happen on shift. Ensuring that relevant colleagues are informed of operational disruptions such as absence, material shortages or other.
-
Handovers – Ensure clear and detailed handovers are carried out professionally between one another and between teams.
-
Standards & Process Improvement – proactively communicate where standards or processes on site on are not clear or insufficient in order to feed into the cycle of continuous improvement. This includes clear insights when lines are signed back into production through sign-off documentation.
-
Labour Planning – expected to manage the short-term horizon (0-4 weeks) labour plan in their area, working with other shift managers to proactively fill gaps where necessary.
Projects
- Receiving – Shift Managers may be asked to provide input into projects at the design or implementation stage, or to gather insights and feedback through their teams.
People Management
-
Direct Reports – this role is responsible for the line management of semi-autonomous operator teams on shift. This includes typical line management responsibilities such as performance management, annual appraisals, absence management, coaching & development planning.
-
Employee Relations – shift managers are expected to carry out disciplinary investigations / hearings and to hear grievances where required in their area.
Continuous Improvement
-
Skills & Knowledge – Has knowledge and understanding of the key principles of continuous improvement and an awareness of the tools to identify and prioritise time, cost and waste losses in the production area and eliminate them; role also requires data collection through teams.
-
Information Input – Ensures the accurate and clear communication of information of loss phenomena from shift teams to days teams through tools such as 5G, 5W1H, 5Why and others.
-
Improvement Ideas – Suggest and implement improvement ideas in the production area.
-
Long Term Improvement Plans – Collaborates with the process engineer, engineering technicians and shift managers to build long term improvement plans for their production area,
Training & Recruitment
-
Training Plans – works closely with the site training team to ensure requirements for their teams are clear and to support in the efficient scheduling of activities.
-
Trainer / Trainee Management – daily management of training activities to ensure they are being completed in line with requirements. Expectation is to intervene with individuals when the training process is not being followed properly or professionally.
ALL ABOUT YOU
-
National school leaver qualifications in Reading and Comprehension, Writing and Mathematics. This will support recording of data, analysis of machine performance and general teamwork skills with an emphasis on good communication.
It would be advantageous to have a background in shop floor roles but is not essential.
Experience Required:
-
Must have an understanding of the end-to-end manufacturing process.
-
Has knowledge and understanding of national Safety and Environmental legislation and company policy, systems and practice relevant to the factory and the legal responsibility placed upon individuals.
-
Strong servant leader, with significant demonstrable experience of achieving sustained success within a manufacturing environment.
-
Has successfully led improvement projects and managed the change and transition process with teams of people.
-
Strong continuous improvement knowledge.
-
Excellent organisation & communication skills.
-
Considerable ability to drive a strong safety culture.
-
Ability to deal with ever-changing fast-paced environment, making quick sound decisions, prioritising and driving changes to the operation in real time
-
Is curious about self-development, proactively and continuously develops self to be the best they can be
-
Should ideally have reasonable mechanical skills to address day to day issues.
This role is ideal for individuals who wish to develop into more senior people leadership roles or technical roles in manufacturing.
Contacts:
-
Manufacturing Manager
-
Production Coordinators
-
Operators
-
Technicians
-
Process Engineers
-
Engineering Manager
-
Maintenance Planner
-
HR
-
ManEx Coordinator
-
Skills Trainer and Skills Coordinator
-
Safety Manager
-
Quality Manager
-
Maintenance Manager
-
Automation Engineers
NOTES
About Unilever
Unilever is one of the world’s leading suppliers of Food, Home and Personal Care products with sales in over 190 countries and reaching 2 billion consumers a day. Unilever has more than 400 brands found in homes around the world, including Dove, Tresemme, Lynx, Lifebuoy, Shea Moisture, Persil, Domestos, Ben & Jerry’s, Magnum, Marmite, The Vegetarian Butcher, Graze and Pot Noodle.
Faced with the challenge of climate change and the need for human development, we want to move towards a world where everyone can live well and within the natural limits of the planet. That’s why our purpose is ‘to make sustainable living commonplace’.
What We Offer
Not only do we offer a competitive salary and pension scheme, we also offer an annual bonus, subsidised gym membership, a discounted staff shop and shares. You’ll have the opportunity to work directly with our renowned and exciting brands in a flexible and hybrid working environment.
Whilst the role is advertised on a full-time basis, we would be happy to discuss possible flexible working options and what this may look like for you. We are a key advocate of wellbeing and offer a variety of support for our people including hubs, programmes and development opportunities. We strive to achieve a family-friendly and inclusive workplace and to, above all, create possibilities for all.
Diversity at Unilever is about inclusion, embracing differences, creating possibilities, and growing together for better business performance. We want to push boundaries, and have the flexibility needed to keep adapting in an ever-changing, more dynamic world. This means giving full and fair consideration to all applicants, regardless of age, disability, gender reassignment, race, religion or belief, sex, sexual orientation, marriage and civil partnership, and pregnancy and maternity.
As part of your hiring journey, we are happy to support requests for reasonable adjustments, to improve your recruitment experience.
To find out more, including more information about our Employee Resource Groups, please click here (https://www.unilever.co.uk/planet-and-society/equity-diversity-inclusion-at-unilever-uki/) .
Recruitment Fraud
Cyber criminals advertise fake job adverts with prestigious employers as a way of stealing information or even defrauding individuals out of money. In the most sophisticated cases, they will set up fake websites, which have a similar address to companies like Unilever. They even conduct fake telephone interviews and then offer candidates a role with the proviso they pay a fee for background checks or to cover work visa costs. These types of attacks are becoming more common as more people are looking for employment in the economic climate.
How is Unilever tackling this?
Many of Unilever’s recruitment sites publish a warning to candidates about recruitment fraud. The Cyber Security team also proactively scan for signs of people setting up fake Unilever sites and act to close them down.
What can I do?
If you become aware of potential recruitment fraud, spot fake Unilever recruitment adverts or fake LinkedIn profiles, report them via Una Live Chat.
Unilever does not accept responsibility or liability for any candidates who are financially impacted by recruitment fraud. Your vigilance is key!
Job Category: Supply Chain
Job Category: Supply Chain
Job Category: Chaîne d’approvisionnement
Job Type: Make Supervisor
Industry: UnileverExperiencedProfessionals
To help us track our recruitment effort, please indicate in your cover//motivation letter where (vacanciesineu.com) you saw this job posting.